The concept of a digital twin has rapidly gained prominence in the Architecture, Engineering, Construction, and Operations (AECO) industry. With the growing demand for smarter infrastructure and efficient asset management, digital twin technology has proven to be an invaluable tool in transforming how we manage the lifecycle of built environments. In this blog post, we’ll explore the concept of a digital twin, its integration with Building Information Modeling (BIM) and Facility Management (FM), and how it has the power to revolutionize the AECO industry.
Understanding the Digital Twin Journey
A digital twin is a virtual representation of a physical asset, encompassing everything from buildings and bridges to industrial facilities. This digital replica captures real-time data, allowing owners, operators, and managers to simulate, monitor, and optimize their physical assets throughout the lifecycle. The digital twin journey is all about bridging the gap between the physical and digital realms to create a continuous feedback loop, ultimately improving efficiency and reducing operational costs.
Voyansi has embraced the digital twin journey, providing a comprehensive solution that guides organizations in leveraging digital twin technology. This journey isn’t merely a one-step process but a holistic transformation that starts from conceptualization and extends to operation and optimization.
Digital twins offer a new paradigm for owners and operators in the AECO industry. By creating a digital counterpart to a physical asset, managers can gain deep insights into how a building is performing, forecast potential issues, and make data-driven decisions to enhance performance.
BIM and Facility Management Integration: The Foundation of Digital Twins
At the core of the digital twin lies Building Information Modeling (BIM) and its integration with Facility Management (FM) software. BIM is a powerful tool that provides detailed information on every aspect of a building’s lifecycle, from design and construction to maintenance and decommissioning. When BIM is integrated with FM, it enables real estate management to take a giant leap forward, offering a powerful combination of data and analytics.
BIM-FM integration allows operators to access digital models that provide information on every component of the building. This means facility managers can have a detailed view of systems, materials, and assets, ensuring preventive maintenance is proactive rather than reactive. The digital twin goes beyond what BIM offers by adding real-time data and operational analytics to create a dynamic, responsive environment for asset management.
With the integration of BIM and FM, owners and operators can experience a seamless way of managing their properties through web-based solutions that are available across different devices. This convenience leads to greater efficiency, reduced costs, and better insights into the day-to-day operation of assets.
Digital Twins for the Operation Stage
According to a recent industry report, the use of digital twins in building operations can lead to an estimated 30% reduction in maintenance costs and a 25% increase in operational efficiency (Source: Building Operations Report). These findings highlight how digital twins can transform the operation stage of a building’s lifecycle.
The operation stage is where the real value of digital twins comes into play. The majority of the lifecycle costs of a building are incurred during its operation. Having a digital twin can significantly lower these costs by providing a level of control and visibility previously unavailable.
In the operation stage, a digital twin acts as a central hub, integrating all relevant data, including maintenance schedules, asset condition, performance metrics, and more. For facility management, this means having a tool that simplifies operations, reduces response time to problems, and provides detailed data to facilitate decision-making.
For example, when facility management teams have access to a digital twin, they can predict when a critical system component is about to fail. The digital twin combines the historical performance data with real-time sensor information, allowing facility managers to identify early warning signs and schedule maintenance accordingly. This proactive approach extends the life of assets and keeps everything running smoothly.
Digital twins are also particularly useful for industrial plant maintenance. With the ability to create a detailed, interactive 3D model, managers can visualize the current condition of plant components and quickly identify areas that need attention. This visual representation provides a clear and concise way to communicate potential issues to other stakeholders, ensuring everyone is on the same page.
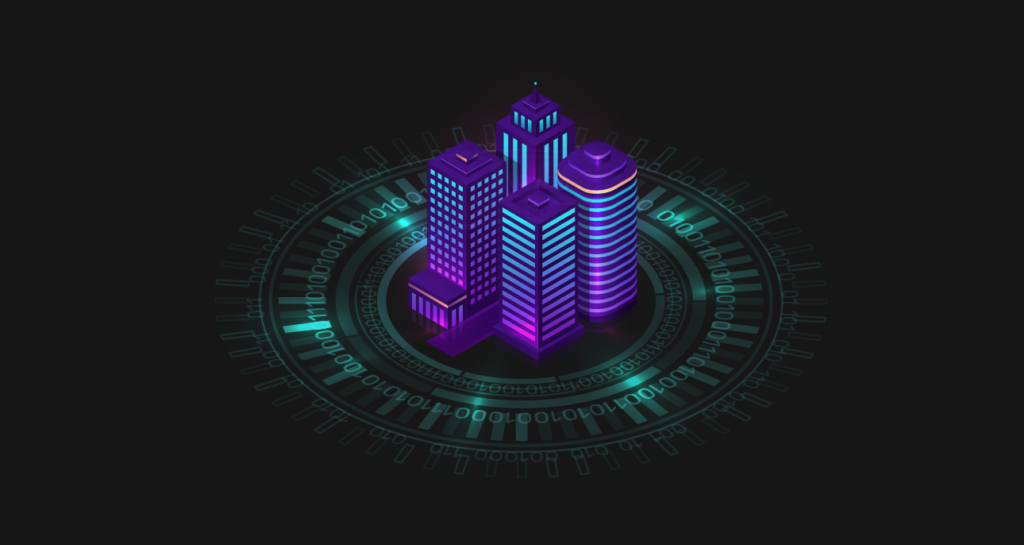
Conclusion
BIM has come a long way since its inception in the 1970s. What started as a digital tool for architects has evolved into a comprehensive platform that touches every aspect of a building’s lifecycle—from design and construction to operations and maintenance. By incorporating multiple dimensions, BIM offers a holistic view of a project, improving collaboration, reducing risks, and driving sustainability.
As BIM continues to evolve, integrating cutting-edge technologies like AI and digital twins, the possibilities for innovation in the AECO industry are endless. For professionals looking to stay ahead, understanding the basics of BIM is crucial. And for those seeking advanced BIM solutions, Voyansi is ready to help you unlock the full potential of this transformative technology.